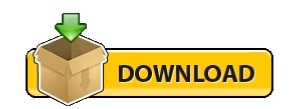

In case of engine failure or EDP failure, System 1 can be pressured by Electric Hydraulic Pump 1, powered by alternating current from AC BUS 2. The HSOV can also be closed manually via a guarded push button on the hydraulic panel. The HSOV will also close automatically in case of engine failure to decrease drag on the engine and make a windmilling relight easier. At 125º C, the Hydraulic Shutoff Valve (HSOV) automatically closes to isolate EDP 1 from System 1. If the fluid reaches 100º C, a HYD 1 HI TEMP caution message is displayed on the EICAS. The return line routes the fluid through another filter and then either through a heat exchanger or directly to the reservoir, depending on fluid temperature. The pump takes fluid from the reservoir, which an accumulator keeps at slight positive pressure, and pressurizes the fluid before sending it through a filter and the plumbing to the various System 1 users.

Hydraulic System 1 is normally pressurized by a mechanical pump driven by the left engine's accessory gearbox. Flight critical systems are powered by three systems, so in the highly unlikely event of two fully independent systems failing simultaneously, the crew will still have at least pitch and roll control. Most aircraft systems that use hydraulic power are powered by at least two of these systems, so the loss of one hydraulic system will not affect most other aircraft systems. All three systems use Skydrol brand hydraulic fluid and are normally pressurized to 3000 psi. System 3 is powered solely by an electric pump, with a second electric pump as backup. They each have an electric hydraulic pump installed as backup in case of engine failure. Systems 1 and 2 are normally pressurized by engine-driven pumps (EDPs), which are connected to their respective engine's accessory gearbox. The JungleBus has three fully independent hydraulic systems. For these reasons, aircraft engineers build multiple independent hydraulic systems into the airliners they design, usually with multiple sources of power for each system. Hydraulic systems have a number of failure nodes: pump failure, loss of power to the pump, loss of fluid, and physical damage to the plumbing so it's unable to hold pressure. For a hydraulic system to work, you need a source of pressure (a pump), a closed system that remains leak-free under significant pressure, and enough fluid to pressurize the system to design pressure. This is possible because fluids are mostly incompressible. Hydraulic systems use a fluid under pressure to do work. Notably missing are the flaps, which are hydraulically powered on many airliners but are electric on the JungleBus. This is the case with many systems on the JungleBus, including all basic flight controls, spoilers, landing gear, brakes, nosewheel steering, and thrust reverser deployment. In these cases, engineers rely on hydraulic systems to do the grunt work. Once you get to airliner weights, though, you find that the forces involved often outstrip the ability of the human muscle to overpower. On most light planes, the hydraulic system is limited to powering the brakes and, in some cases, retractible landing gear. I hope that by next time I have recurrent ground school, I have a nice collection of posts to come back and read rather than poring through AOM-II for hours on end until my eyes bug out. Those with JungleBus experience are welcomed to add anything I forget or correct my mistakes. They won't be in any particular order today I've randomly chosen to begin with a dissertation on the Hydraulic System. With that in mind, I'll be writing occasionally posts on various JungleBus systems. In my experience, the best way to learn aviation knowledge is to teach it. Since then I've gone back and studied on my own a few times, but I still feel like I could benefit from a more intimate knowledge of JungleBus systems. I've mentioned a few times that NewCo's initial training program was a bit, ahem, basic, and that I felt somewhat underprepared in the area of systems knowledge when I first got on the line.
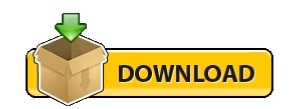